COVID-19 Ushers in New Era of Touchless Coffee Equipment and Sanitary Solutions
COVID-19 has sparked a flurry of demand for touchless solutions to protect the returning workforce from spreading the virus. With safety as paramount to today’s consumers as convenience and quality, suppliers have responded by offering technology updates and new equipment solutions to help operators serve their clients. Operators can help employers keep their employees on-site and feeling appreciated by continuing to safely deliver office coffee service (OCS) as the perennial must-have workplace perk.
“Offices, cafes and restaurants have been closed for months due to quarantine regulations, which means most people have been spending less time in public places drinking coffee and more time at home,” said Luke Webster, director of business development for Newco Enterprises Inc., based in St. Charles, Mo. “Only recently have businesses started to open back up.”
Rising to the Challenge
Touchless equipment and systems have become basic necessities for operators as they revisit their accounts. Newco and its partners have been quickly adapting to serve customers in a way that complies with U.S. Centers for Disease Control and Prevention (CDC) guidelines to combat the pandemic.
“I hope things will return to somewhat normal, but I don’t think they will ever be the quite [the] same,” Webster commented. “And the trends that we see during COVID-19 will change how most people do business.”
One of the biggest challenges Newco faces as a manufacturer in the new world of COVID-19 is getting new ideas to the market quickly, while also delivering high-quality, depend- able products that ensure its customers’ success.
“We do this by investing in new technologies and getting creative,” he said. “At the same time, we make it a point to listen to our customers, find out what exactly their needs are and how we can develop products to help them. Our goal is to have a broad assortment of solutions to fit the needs of our customers as they navigate what is right for them in a constantly changing environment.”
Newco Touchless Solutions is Newco’s response to the recent changes in the industry, encompassing products and tips that help reduce — or, in some cases, eliminate — touch- points on brewers and equipment.
Webster noted that there is no shortage of technology to aid in this endeavor, including Bluetooth, WiFi, Near Field Communications (NFC) and QR codes. “The key is fitting the right technology to the right application so that it is effective and efficient,” he stated.
Newco’s Bistro Touch liquid specialty beverage brewers now include QR code technology to allow customers to choose and customize the size and strength of each drink touch-free. The Bistro Touch delivers specialty drinks in a matter of seconds by combining on-demand liquid coffee with powdered milk and chocolate.
To use the QR feature, the user places the cup on the drip tray, scans the QR code with their smartphone camera app and then chooses a drink from the menu, along with drink size and strength on their phone’s screen. After selecting “next,” a drink QR code pops up that initiates brewing when faced to the machine’s camera. Retrofit kits are also available for existing equipment in the market.
Safety First
Additionally, Newco’s large, “no touch handle” can replace a Tomlinson faucet handle on a dispenser, eliminating the need to touch the handle by simply pressing the cup against it to easily dispense coffee or tea.
Newco is also providing a printable card (see page 28) to display next to machines with tips to prevent the spread of COVID-19 by cleaning and disinfecting surfaces, especially touchpoints on its single-cup pod brewers. This includes using a stylus on touchscreen displays, using a pod package itself as a stylus, or using the wrapper as a barrier to tap the brew button.
Arjan de Groot, vice president North America for Bravilor Bonamat, a Dutch manufacturer with U.S. operations in Aurora, Ill., said his company has been working closely with its operator customers to meet changing needs.
“While the initial wave of office lockdowns brought new client onboarding to a standstill, our clients are experiencing an uptick again in new equipment placements, replacement, refurbishment and updates,” de Groot was pleased to report.
However, he emphasized, they still face struggles. New business opportunities are hard to come by and existing accounts are not generating the same returns as they were pre-COVID.
“Our focus pre-COVID was on equipment value and ROI. The bean-to-cup demand was growing rapidly and we wanted to offer alternatives to costlier bean-to-cup equipment designed to serve 50 to 200 individuals a day at a minimum,” he recalled. “Finding these types of opportunities was not always easy pre-COVID and certainly isn’t today. With smaller, value-priced equipment like our SEGO, our operators are finding it easier to justify that type of equipment purchase as the demand for a fresh-brewed cup of coffee remains.”
Bravilor Bonamat is launching a touchless app for its SEGOTM bean-to- cup machine that works via NFC technology, which can be incorporated into existing equipment without the need for a cellular or internet connection to the machine.
“With this technology, we are making sure our clients are not tied to any fixed subscription or data cost affecting their bottom line,” de Groot explained. “And, based on the success of ordering and payment apps across the food and beverage industry, we believe in the added benefit of providing a touchless ordering app and creating successful returns on investment.”
Beyond The Basics
Astute operators are positioning themselves as break room consultants, de Groot noted, presenting a multifaceted approach to break room hygiene, from sanitizers and dispensers to reducing touchpoints of product and equipment.
“Our goal is to stand by our operators through offering a multitude of options and support,” he stated.
Bravilor, together with a distributor partner, is offering anti-microbial touchscreen films for its equipment that inhibits bacterial and viral growth. It also designed a high-end, stainless steel, foot-operated dispenser for sanitizers, which is built to last and complement any break room, lobby or office.
Bunn-O-Matic, based in Springfield, Ill., is another manufacturer quick to respond to new demands with its new VirtualTOUCH touchless beverage dispensing experience, powered by its BUNNlink® cloud- based solution. Fully automated via smartphone, it provides access to a full beverage menu and intuitive, step-by-step instructions, while reducing shared contact points.
The user simply scans the QR code, selects the location, and then scans the QR code on the machine with a smartphone. A mobile web page then opens with simple prompts, starting with placing a cup under the spout and entering the code shown on the coffee machine touchscreen, and then the drink process unfolds.
VirtualTOUCH is currently available with Bunn’s Sure Immersion® 220 and 312 and Fast Cup® brewers, with additional models coming soon. It works with 365 Retail Markets’ 365Pay app for simple integration into a micro market and accepts 365’s Global Mar- ket Account payment.
The popular Serenade® single-cup brewer is now equipped with Bunn’s VirtualTOUCHTM touchless beverage dispensing technology, enabling operators to safely and easily deliver freshly brewed Starbucks® coffee on-site.
In-House Coffeehouse
“Today’s workforce seeks safety along with quality and convenience when they come into the office. Now our customers can deliver a touchless Starbucks® bean-to-cup coffee experience that exceeds employee expectations to keep them on-site throughout the day,” said Melissa Henshaw, senior vice president of Nestlé Coffee Partners – Solutions Lab, an alliance between Nestlé and Starbucks that delivers the Starbucks bean-to-cup experience in the OCS channel. “They can also enjoy Starbucks® iced coffee, hot cocoa or chai, all in one turnkey solution. The Serenade® Single-Cup Brewer with VirtualTOUCHTM technol- ogy safely delivers the freshly brewed Starbucks® coffee they know and love, right from their smartphones.” (Learn more here https://bit.ly/2YualJN
Karalynn McDermott, senior vice president, market development for Bunn-O-Matic, explained that the company had developed BUNNlink® cloud connectivity to enable remote equipment monitor- ing for operators. When COVID hit, the brewer manufacturer pivoted the technology to be consumer-facing with the creation of the Virtual- TOUCH touchless experience.
“We think it will have staying power beyond the pandemic,” she predicted. “We all use our personal devices as an ‘arm extension,’ and using it through a QR code is super popular. It integrates with other apps, taking it a step further so they can come into a micro market and use their phone for everything. The industry has an opportunity because coffee consumption had been down in the workplace and now it can increase because when employees get to the workplace, they want to stay put.”
Layer Of Protection
Beyond VirtualTOUCH, Bunn has rolled out a suite of solutions to enable operators to reduce the risk of COVID-19 spread on high-frequency touchpoints on their existing brewing equipment and servers. Its anti-microbial films, available in full sheets or pre-cut sizes, cover common contact points and allow equipment to function normally without leaving a sticky residue when replaced. Anti-microbial film can be applied to touchscreens, touch switches, membrane switches and handles.
Bunn’s stainless-steel faucet adapters attach to Bunn Soft Heat®, ThermoFresh® and tea dispensers, allowing for easy cup-push service, eliminating hand contact.
Bunn servers, new or old, can be outfitted with push-style faucets that emphasize clean contact. These faucets are easy to install and offer a clean-contact solution for beverage dispensing. The company also offers anti-microbial replacement parts for high-frequency contact points such as faucets, handles and dispense membrane switches. Anti-microbial faucets, handles and films can easily be self-installed, while anti-microbial membrane switches require technician installation.
Additionally, Bunn equipment that relies on handles can now be a reliable way to dispense beverages while ensuring clean contact, with Tap-KinsTM biodegradable and recyclable sleeves that users can easily take from a dispenser, slide over any handle, and discard without any direct surface contact. The sleeves are sold by the case; 300 sleeves per roll and 10 rolls per case.
Featured here are only a handful of the many equipment providers helping operators rise to COVID-19’s challenges with the creativity and perseverance upon which office coffee service was built.
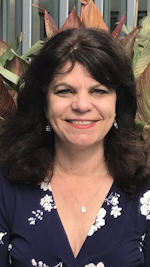
Emily Jed
Emily Jed is a business journalist who has devoted much of her career to covering the convenience services industry. She is a contributing editor to Automatic Merchandiser/VendingMarketWatch.com.