What would happen if your route truck broke down? Perhaps you are one of those operations that has a spare vehicle that the driver can use to service his or her accounts? Perhaps there is a reliable repair shop that can come to the operation’s aid quickly? Unfortunately, the answer to both these questions is generally “no” leaving the operator without a vehicle. This means accounts won’t get serviced, the operator’s customers may become angry and most importantly, there won’t be any collections for that day.
To add insult to injury, when the mechanic is finally able to look at the operator’s vehicle, the report comes back that there is no oil in the crankcase and the engine is cooked. Now what? Replacing an engine is costly, not to mention the additional expense incurred for a rental truck for the driver to use while his or her vehicle is being fixed. All of this could have been avoided by understanding one simple truth — the route truck is the life blood of an operator’s company. Keeping the vehicle in good running order should be one of an operator’s highest priorities.
Schedule regular checks
Let me ask a simple question: Who is checking your route vehicles? Is it the route driver? Is it you, the operator? If an operation is large enough, perhaps there is support staff — is one of them checking? In the end, someone should be assigned to check each vehicle on a regular basis and a log of those checks should be made. Allow me to offer some suggestions.
1. Individual vehicle files
Give each truck a number and then create a folder for every vehicle in the fleet. Within that folder operators should keep a log that shows the date and mileage every time that particular vehicle was checked. A record of what was found, if anything, and what work was performed at that time should also be noted. In that same folder, operators should keep a copy of all receipts for parts purchased and outside repair work performed. This way operators can easily go back and check how much money they are spending on each vehicle.
2. Minimum service schedule
The basic maintenance for any vehicle should be regularly changing the oil, checking all the fluids, examining wiper blades and ensuring interior and exterior lights function normally. I’m sure that there are mechanics out there that will add to this list but this is a very basic list to start the process and keep vehicles in good running condition.
The regular oil change is a must no matter what else operators may or may not do. Look for a repair shop near the warehouse where drivers can take the vehicle for an oil change and fluids check. If operators have more than one vehicle, they can likely work out a deal to bring in all their vehicles at once, every 3 months, to get the basics done. This is what our company did. We negotiated with the local Jiffy Lube to set up a day to bring all our vehicles in to get them checked. We continued to do this until we grew to over 20 vehicles, at which time we decided to hire our own mechanic to take care of our fleet from changing oil to changing engines. After the initial start-up costs of the first 2 years, the in-house mechanic more than paid for himself by what we saved.
I know most operations are not large enough to hire their own mechanic. Instead, operators can create a program that will allow them to stay on top of vehicle maintenance. This is what will save them money.
3. Weekly driver checklist
Another important maintenance component is to create a checklist for drivers to fill out on a weekly basis or anytime something is wrong with the truck. The checklist can be small, perhaps half a sheet of standard paper. On the paper, type or write a list of items that need to be checked. Leave a space next to each item where the driver can place a checkmark and any comments. Some items to consider for the checklist are: check oil and other fluids, windshield wipers, headlights, turn signals, back lights, brakes, battery, tires, mirrors, locks, etc. Make sure to put the truck number at the top and leave room for the date and mileage. Mileage can serve a dual purpose, first to see when repairs were made and second to see how much that truck is traveling each week or month. If operators find one vehicle is traveling a great deal more miles than another, they might want to consider switching it with another truck in the fleet every 6 months. This will ensure wear and tear is more evenly distributed.
4. Wash the vehicle bi monthly
I also highly recommend one other item and that is a wash. Yes, a wash. Always remember how a vending operation needs to look to customers. Believe me, a clean truck says a lot about an operator and his or her company. Get a service to come to the warehouse every 2 to 3 weeks, to wash all the vehicles. It will be quick, easy and not very expensive.
By now, I’m sure many operators are saying ‘wow that’s a lot to do for just one or two trucks.’ Yes. It can be, until you think of the alternative. Besides the obvious costly repairs a vehicle may have when it has been neglected, imagine a driver gets in an accident. When the police or insurance company is determining fault, it may come out that the vehicle turn signal wasn’t working, the brake pads were worn or the windshield wasn’t as clean as it should have been. This may impact findings and ultimately lead to fines or increased insurance premiums. Operators will be able to rest a little easier if they can present the insurance company with a folder on the vehicle in question that documents all the maintenance done with the date of completion. Everyone involved can then eliminate vehicle negligence as a possible cause of the accident. A vending business relies on its delivery vehicles — give preventative maintenance a high priority.
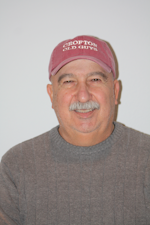
Dominic Finelli
Dominic Finelli is 43-year veteran vending operator in the Washington D.C market. Along with his partner/brother-in-law, John Sartori, he helped grow a family start-up, Custom Vending, to 30 routes. Finelli earned a degree in accounting from Benjamin Franklin University, was a 3-time recipient of the NAMA Chairman's Legislative Award and the 2004 Operator of the Year. Finelli served 23 years as a director of the MD/DC Vending Association, and 10 years as the president. He sold his vending company in 2011. Finelli can be reached at [email protected].